Non-Destructive Testing (NDT)
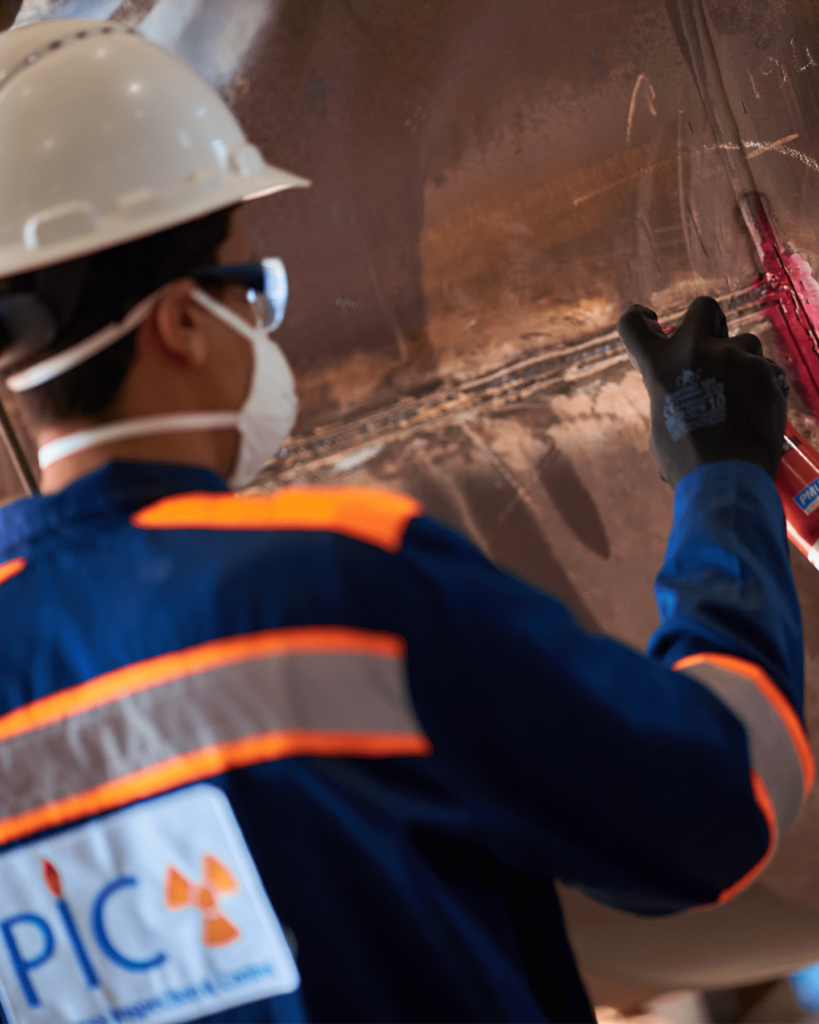
Services
Welcome to PIC, where our unwavering commitment is to deliver exceptional Non-Destructive Testing (NDT) services, utilizing a blend of advanced conventional techniques to surpass the highest standards set by our clients.
Specializing in assessing the integrity of materials and metal structures, we offer a comprehensive suite of NDT services throughout the entire equipment lifecycle, from production to maintenance.
- Conventional Non-Destructive Testing Services
- Advanced Non-Destructive Testing Services (Advanced NDT)
- Ultrasonic Detection of Buried Tanks
Conventional Non-Destructive Testing Services
- Visual Inspection (VT)
- Radiographic Testing (RT)
- Ultrasonic Testing (UT)
- Penetrant Testing (PT)
- Magnetic Particle Testing (MT)
Advanced Non-Destructive Testing Services (Advanced NDT)
- Time-of-Flight Diffraction (TOFD) Testing
- Multi-Element Ultrasonic Testing (Phased Array) (PA)
- Tank Bottom Inspection
- Endoscopic Inspection for Hard-to-Reach Areas
- Eddy Current Testing (ET)
Ultrasonic Detection of Buried Tanks
Visual Testing (VT):
In accordance with current standards, VT serves as the initial step to evaluate material quality without altering its properties, forming a crucial foundation for our in-depth inspections.
Radiographic Testing (RT):
Critical for providing a detailed view of internal defects, radiography ensures the quality and reliability of industrial components, detecting structural anomalies without compromising material integrity.
Ultrasonic Testing (UT):
Essential for a precise evaluation of material integrity, ultrasonics contribute to thorough inspections, optimizing result reliability by detecting internal defects with sensitivity.
Penetrant Testing (PT):
Integrated seamlessly into production lines, PT is a cost-effective method offering high reliability in detecting various surface defects, ensuring asset and personnel safety.
Magnetic Particle Testing (MT):
Widely used across sectors, magnetic particle testing enables rapid inspection of components with simple or complex geometries, ensuring the quality of ferromagnetic materials.
Time of Flight Diffraction (TOFD):
Essential for rapid weld inspections, TOFD ensures comprehensive coverage of critical areas.
Phased Array Ultrasonics (PA):
Our use of Phased Array technology offers increased flexibility in non-destructive testing, allowing for more precise inspections through electronic control of the ultrasonic beam.
Tank Bottom Inspection:
PIC’s tank bottom inspection incorporates advanced techniques to precisely map corrosion and identify at-risk areas. Using technologies such as MFL, our experts conduct a thorough evaluation, ensuring early detection of corrosion defects, optimizing maintenance, and ensuring the durability of storage structures.
Endoscopic Inspection for Hard-to-Reach Areas:
PIC’s Endoscopic Inspection provides an effective solution for inspecting hard-to-reach areas. This method uses endoscopes equipped with cameras to explore restricted spaces, ensuring detailed inspection of industrial equipment. PIC’s Endoscopic Inspection guarantees accurate assessment, enabling informed decision-making for maintenance and facility security.
Eddy Current Testing (ET):
PIC’s Eddy Current Testing goes beyond its reputation for easy calibration and high testing speed. This innovative method excels in efficiency, even through layers of paint and non-conductive coatings, eliminating the need for prior stripping. Its ability to detect through-thickness defects makes Eddy Current Testing indispensable for various applications.
Particularly suited for inspecting heat exchanger tubes, Eddy Current Testing plays a crucial role in maintaining the integrity of these critical components in industries such as petrochemicals and energy. This method offers a precise solution, contributing to the reliability and safety of heat exchangers. Beyond its application in heat exchanger tubes, Eddy Current Testing remains a versatile technique, offering significant advantages for various inspections without compromising result quality.
Our expertise extends to ultrasonic detection of buried tanks, providing solutions for leak testing, detection of internal valve leaks, and identification of void/gas leaks. This methodology ensures the safety of tanks used for the storage of fuel, chemicals, or water.
Feel free to contact us to learn more
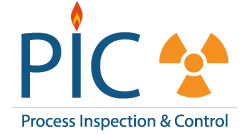